Faserzementrückstände als Rohstoffsubstitut in der Zementindustrie

(24.8.2010) Die neue europäische Abfallrahmenrichtlinie ist am 12. Dezember 2008 in Kraft getreten und die Bundesrepublik Deutschland ist nun in der Pflicht, ihr Abfallrecht bis Ende 2010 den europäischen Vorgaben anzupassen. Die neue Richtlinie definiert die Abfallhierarchie ...
- Vermeidung
- Wiederverwertung
- Recycling
- Andere Verwertung
- Beseitigung
Gleichzeitig ist aktuell (noch?) die Recyclingquote für Bauabfälle bis 2020 auf 70% festgelegt (vergleiche mit Beitrag "Bundesgütegemeinschaft Recycling-Baustoffe begrüßt gefordere Erhöhung der Recyclingquote" vom 22.8.2010). Forderungen, denen sich die Faserzementindustrie vom Beginn der Entwicklung asbestfreier Produkte Anfang der 80iger Jahre stets gestellt hat. So wurden Produkte aus Rohstoffen entwickelt, die den Forderungen nach Wiederverwertung und Recycling wie gefordert genügen können. Im Folgenden wird eine Wiederwertung von Rückständen aus der Faserzementherstellung in der Zementindustrie beschrieben, wie sie von einigen europäischen Faserzementherstellern seit mehreren Jahren erfolgreich praktiziert wird.
Zusammensetzung von Faserzement
Die Rohstoffauswahl zur Herstellung von Faserzement (FZ) orientiert sich an Nachhaltigkeit und Wiederverwertbarkeit. Naturgehärteter Faserzement besteht aus ...
- ca. 80% Portlandzement als Bindemittel,
- ca. 2% Armierungsfasern (organische Fasern aus Polyvinylalkohol),
- ca. 3% Prozessfasern (Zellstofffasern aus ökologischer Bewirtschaftung),
- ca. 10% Kalkstein gemahlen als Zusatzstoff und
- bis zu 5% weiteren Zusatzstoffen (z.B. amorphe Kieselsäure aus der Rauchgasreinigung)
Zur Ressourcenschonung werdne Produktionsabfälle, soweit wie möglich, dem Produktionsprozess wieder zugeführt. Diese Vorgehensweise zeichnet alle Produktionsstandorte der deutschen Faserzementindustrie aus.
Die nachfolgend beschriebenen Abläufe betreffen konkret den Produktionsstandort Neubeckum der Eternit AG Deutschland. An diesem werden sowohl Dach- als auch Fassadenplatten aus Faserzement hergestellt.
Faserzementabfall: weich und hart
Bei den verschiedenen Herstellungs- und Veredlungsprodukten können unterschiedliche Sorten von Abfall auftreten. Beim Hatschek-Prozess (dem Verfahren zur Herstellung von Faserzement benannt nach Ludwig Hatschek, dem Gründer der Eternit-Werke in Oberösterreich) tritt ausschließlich Weichabfall auf, der aufbereitet der Rohstoffmischung wieder zugeführt wird. Er ist für die Abfallbilanz von untergeordneter Bedeutung. Demgegenüber steht der Hartabfall.
Insbesondere in den Veredelungsstufen (Zuschnitt, Beschichtung) kam es auf Grund von Qualitätsaspekten und Prozessgegebenheiten zu erhöhten Ausschussraten. Durch den Einsatz moderner Sägemaschinen, Fräsanlagen und Bohrautomaten in Verbindung mit moderner Prozessteuerung gelang es, die Ausschussrate zu reduzieren. Die durch die Bearbeitung entstehenden Stäube werden mittels Entstaubungsanlagen abgeführt und in speziellen Behältern gesammelt. Der so gefasste Staub kann innerhalb anderer Produktionsschritte wiederverwendet werden.
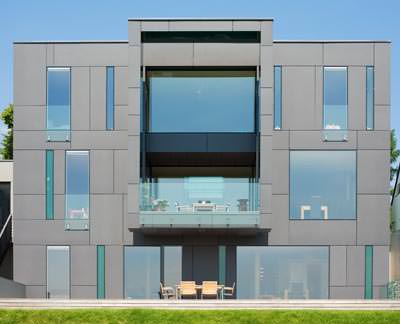
Zur Formgebung der kleinformatigen Dachplatte kommt eine Vielzahl von unterschiedlichen Stanzen zum Einsatz. Die bei der Bearbeitung entstehenden Stanzreste werden in Behältern gesammelt und können, nachdem sie aufbereitet wurden, intern verwertet werden.
In letzter Konsequenz kann aber nicht die gesamte Menge an Produktionsabfällen intern verwertet werden. Daher wurden etliche externe Verwertungsmöglichkeiten für das FZ-Material auf dem Sektor des Baustoffrecyclings auf Einsetzbarkeit hin überprüft. Auf diesem Gebiet gibt es bereits seit mehreren Jahren praktikable Lösungen.
Um aber wirkliche Synergieeffekte im Fokus auf Ressourcenschonung zu erzielen, blieb eigentlich nur der Schritt, diesen Produktionsabfall als Ausgangsmaterial bzw. als Rohstoffsubstitut zu erkennen und einem entsprechenden (externen) Herstellungsprozess zuzuführen.
Kooperationen mit der Zementindustrie
Hauptbestandteil der FZ-Produkte ist, wie bereits erwähnt, das Bindemittel Portlandzement. Daher war es naheliegend, Zementhersteller als Kooperationspartner zu gewinnen. Nach Gesprächen mit relevanten Kooperationspartnern und entsprechenden Vorprüfungen der einzusetzenden mineralisch gebundenen Rückstände, begann Anfang 2005 das eigentliche Antragsverfahren gem. §§ 6 und 16 Bundesimmissionsschutzgesetz (BImSchG) auf Seiten des Zementherstellers HeidelbergCement AG für das Zementwerk Ennigerloh.
Nachdem keine nachteilige Auswirkung auf die im Bundesemissionsschutzgesetz genannten Schutzgüter zu besorgen war, erteilte die zuständige Bezirksregierung im März 2005 eine entsprechende Genehmigung zum Einsatz mineralgebundener Rückstände aus der Faserplattenproduktion. Festgelegt wurden in dem Bescheid:
- Menge des Stoffes: 6.000 t/a durchschnittlich 2 t/h
- Stoffbezeichnung: Abfallschlüssel 101311 "Abfälle aus der Herstellung von Verbundstoffen auf Zementbasis"
- Herkunft des Stoffes: Eternit AG, Werk Neubeckum
Daraufhin konnte zeitnahe mit der regelmäßigen Anlieferung von faserzementhaltigen Dach- und Fassadenplatten als Rohmaterialsubstitut begonnen werden.
Die Anfallmengen des FZ-Materials liegen zwischen 10% bis 13% der Gesamtjahresproduktion an Faserzementprodukten des Werkes Neubeckum, was einer Tonnage von ca. 6.000 to bis 8.000 to entspricht. Die derzeitige Wiederverwertungsrate im Zementwerk Ennigerloh liegt bei ca. 92%. Da laut Genehmigungsbescheid die Eintagsmenge in das Zementwerk Ennigerloh auf 6.000 to/a limitiert ist, können die überschüssigen Mengen an FZ-Material auf einem extra Lagerplatz im Werk Neubeckum zwischengelagert werden.
Verfahrensbeschreibung
Das FZ-Material aus der Fassadenplattenproduktion besitzt das größte Format. Um das FZ-Material für die Anlage im Zementwerk handhabungsfähiger zu machen, muss dieses vorgebrochen werden. Unterjährig wird mit Hilfe einer mobilen Brecheranlage der Recyclingprozess der ersten Stufe eingeleitet. Das Recyclingmaterial wird auf die Korngröße < 50 mm vorgebrochen. Staubemissionen während des Brechvorganges werden durch Wasserbedüsung gemindert.
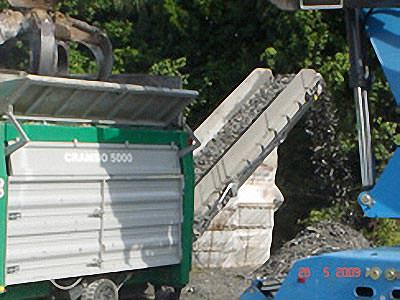
Der Transport des gebrochenen Recyclingmaterials zum Zementwerk erfolgt durch Abrollcontainer. Diese werden mit Hilfe eines Radladers beladen. Durch Zwischenlagerung und Weitertransport innerhalb des Zementwerkes wird das Material der Weiterverwertung zugeführt.
Das recycelte mineralisch gebundene FZ-Material kann in Mischung
mit dem gewonnenen Kalkstein wieder zur Zementherstellung genutzt werden. Es
fallen keine Produktions- oder Recyclingrückstände an. Das Recyclingmaterial
wird im Steinbruch des Zementwerkes Ennigerloh mit dem Kalkstein vermischt und
danach der Brecheranlage und
den
weiteren Verarbeitungsschritten zugeführt. Die ursprünglichen Faserzementplatten
durchlaufen somit denselben Aufbereitungsprozess wie der eingesetzte Kalkstein.
Der Anteil an Recyclingmaterial im Kalkstein kommt auf einen Wert von ca. 0,45%. Aufgrund dieses geringen Anteils im Rohmaterial sind für die Klinkerproduktion (Zementklinker wie im Bild rechts, nicht zu verwechseln mit Klinkersteinen) keine wesentlichen Änderungen festgestellt worden.
Weitere
Informationen zu Faserzement-Dachplatten und -Fassadenplatten sowie ihrer
Ökobilanz (Life Cycle Assessment) können per
E-Mail an Eternit
angefordert werden.
siehe auch für zusätzliche Informationen:
- Green Sense Concrete Technologie jetzt auch in Europa verfügbar (5.3.2014)
- Forscher aus Sankt Augustin suchen nach klimaschonenderem Zement (24.10.2013)
- Bundesregierung will Rohstoffproduktivität maßgeblich steigern (15.4.2013)
- Preiswerter Zement aus Philadelphia verspricht 97% weniger Energieverbrauch (5.7.2012)
- Deponierung contra Recycling und Verwertung? (28.5.2012)
- weitere Details...
ausgewählte weitere Meldungen
- Klimaschonender Zement Celitement bekommt Pilotanlage (24.8.2010)
- Bundesgütegemeinschaft Recycling-Baustoffe begrüßt Erhöhung der Recyclingquote (22.8.2010)
- REACh und Recycling-Baustoffe (7.6.2010)
- Neue Eternit Website (2.3.2010)
- Von der Berichterstattung vergessenes Thema? Sondermüll beim Bauen und Sanieren (7.2.2010)
- Von 50 auf 50 Millionen Stoffarten im Bauwesen (7.2.2010)
- "Grüner" Zement Celitement hinterlässt kleinere "ökologische Fußabdrücke" (4.1.2010)
- Zwei-Komponenten-Bewehrungsfaser verschafft Beton zusätzliche Duktilität (4.1.2010)
- Holcim Studienpreis für Nachhaltigkeit vergeben (25.10.2009)
- Bessere Verfahrenstechnik für Dachplatten aus Faserzement (19.8.2009)
- Einfamilienhaus flächenbündig in Glas und Faserzement gekleidet (30.7.2009)
- Betondachsteine mit hervorragender Ökobilanz (7.3.2008)
- Ersatzbrennstoffnutzung in Zementwerken (5.6.2007)
- Hochofenzement senkt Energiebedarf und CO₂-Emissionen (17.5.2006)
siehe zudem:
- Zement, Dachsteine, Dachdeckung, Fassaden-Verkleidung und Bauforschung auf Baulinks
- Literatur / Bücher zu den Themen Betonbau und Bauen bei Amazon